What Makes Plate Rolling A Powerful Asset For Industrial Projects?
Industrial sectors often rely on metal components that require precise shaping without error or delay, especially when these parts must support heavy loads or resist pressure in harsh conditions.
Many modern infrastructure designs include round or curved steel elements that play a vital role in performance, efficiency, and durability. As a result, plate rolling has become a key process in helping industries meet the demands of strength, form, and cost-efficiency.
The ability to shape large metal sheets into perfect cylinders or arcs using mechanical rollers has made this method an essential solution for heavy fabrication needs. It has become a preferred forming technique due to its consistency, scalability, and usefulness across multiple sectors.
Streamlined Metal Shaping With Greater Control
Plate rolling offers an efficient path for transforming flat sheets of metal into well-shaped cylindrical or curved forms without breaking, cracking, or weakening the material during the process. By feeding the sheet between pressure-driven rollers, the operator can control both the shape and tightness of the bend with high precision.
Unlike outdated methods that require welding separate arcs or segments, this technique creates seamless structures in one continuous cycle, which reduces both labor time and the risk of errors or weak joints. By producing consistent results through fewer steps, plate rolling ensures that each part meets required design standards without further finishing.
Ideal for High-Strength Applications Across Multiple Industries
Many heavy industries need components that do not bend, crack, or warp under pressure, which makes plate rolling ideal for tanks, pressure vessels, wind towers, and piping systems used in power generation or marine engineering.
As the rollers apply steady force over the surface, the metal compresses slightly at the molecular level, making the curved result stronger than a jointed counterpart. Components formed using this process often outperform those shaped with cutting or welding in terms of both structural integrity and durability.
Time and Labor Advantages in Large-Scale Fabrication
Traditional forming methods often involve multiple steps, including cutting, welding, shaping, and polishing, each requiring time, attention, and skilled labor. Plate rolling offers a direct path from raw sheet to finished part, which helps reduce hours spent in production while increasing throughput for high-demand projects.
Since every step happens in a single pass, teams move faster through timelines, improving project delivery without reducing quality. The simplicity of the method also removes the need for complex post-processing, which adds cost and slows down completion schedules.
Efficient Use of Resources with Less Waste
Minimizing waste has become a goal for industries aiming to cut costs while maintaining quality, and plate rolling meets this need by using full sheets in a highly controlled manner that reduces scrap.
When fewer off-cuts remain and shapes come out correctly the first time, businesses can stretch material budgets and keep the workflow smooth. The need for extra tools or attachments also decreases, lowering both operational expenses and time lost.
Versatility in Material and Design
Plate rolling works on various metals such as steel, aluminum, and copper in multiple thicknesses, making it suitable across industries with different design needs. Companies involved in construction, shipbuilding, aerospace, energy, or transport rely on this process for projects requiring strength and accuracy. The same machine handles different tasks with minimal adjustment, making it valuable in metalworking environments.
Harvey Brothers Inc.., based in Cincinnati, Ohio, provides accurate and
reliable plate rolling services that help industrial clients finish projects faster, safer, and with cleaner results by delivering curved metal parts made to exact design needs.
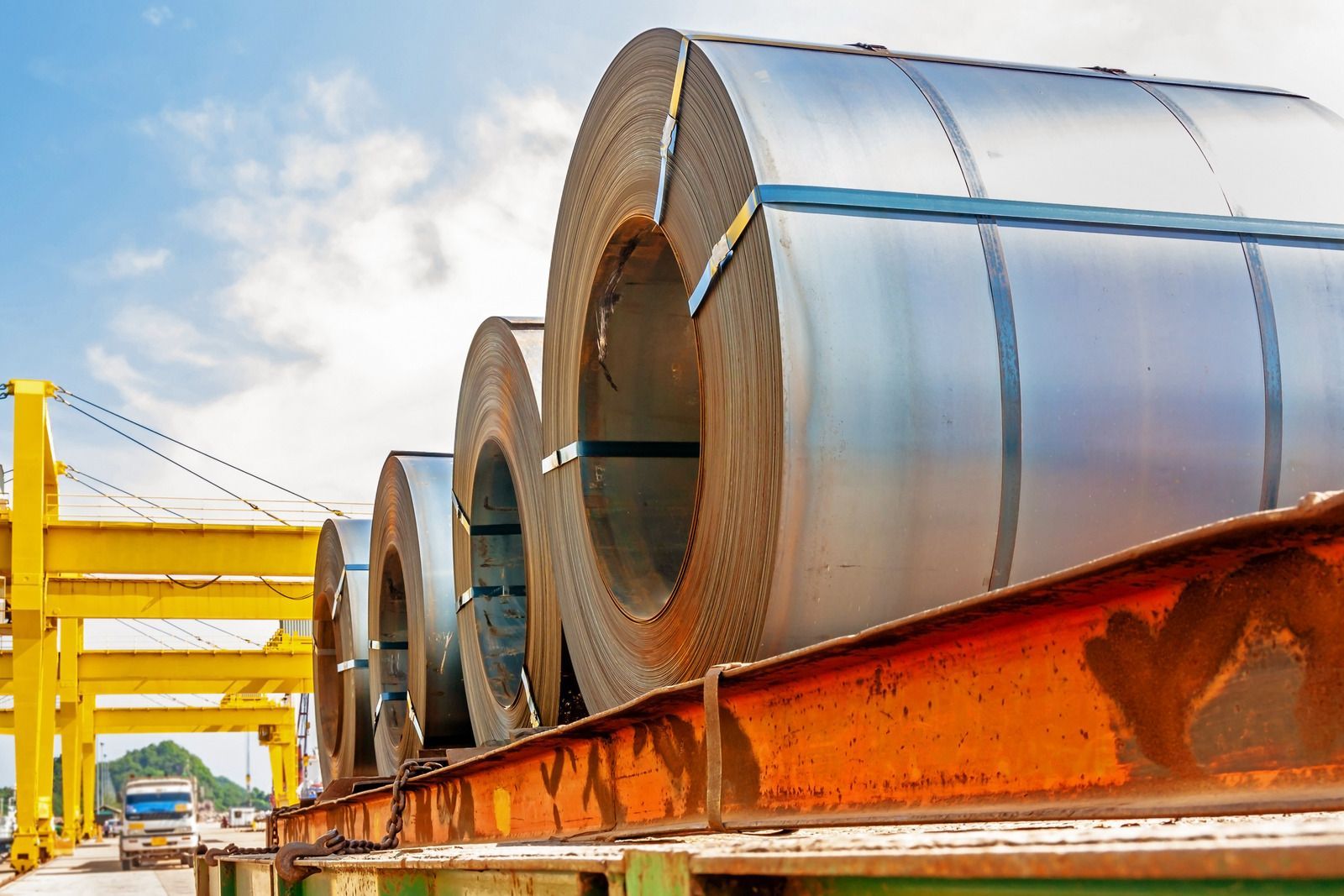
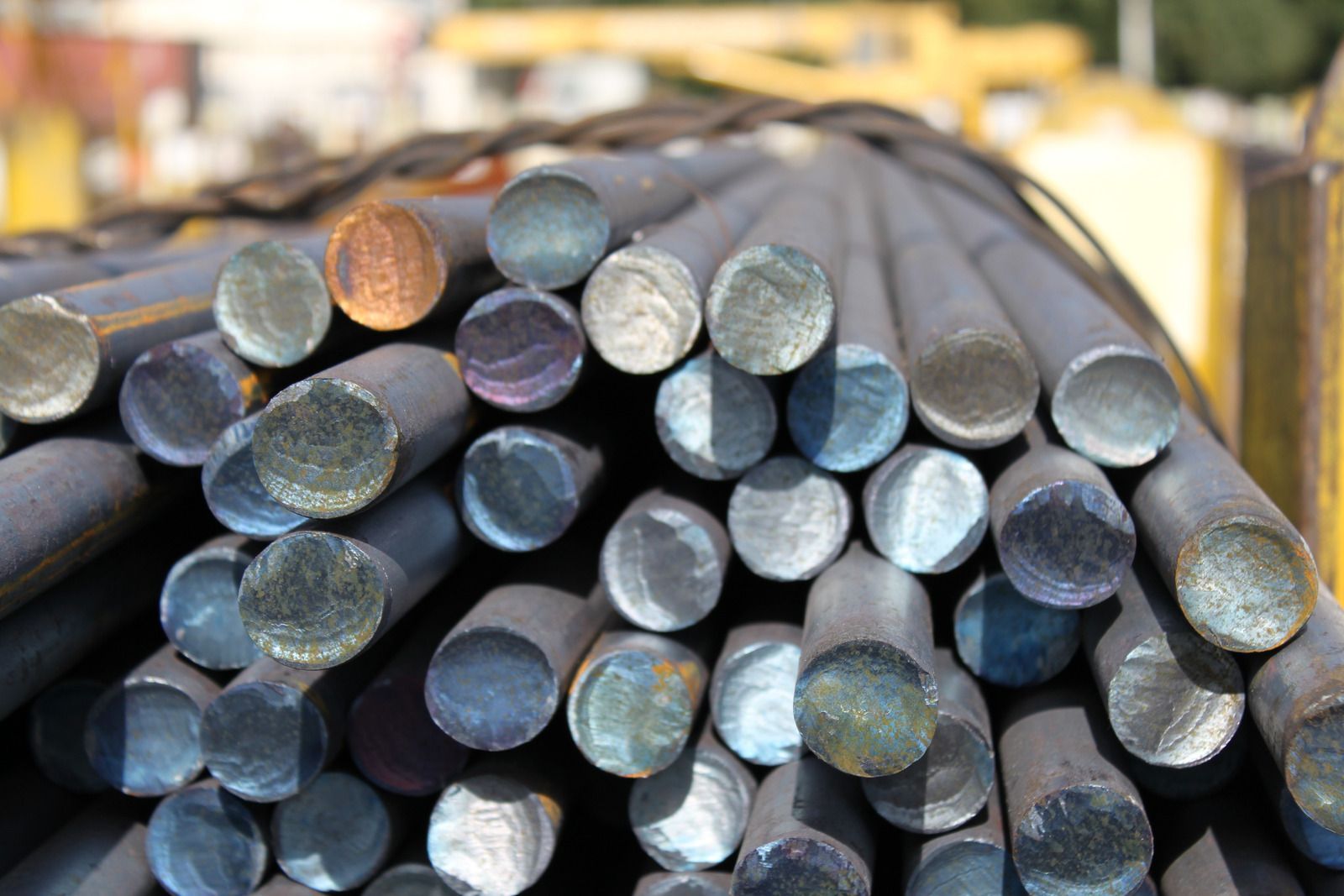